6S管理是一种广泛应用于生产和车间环境中的管理模式,旨在通过整理、整顿、清扫、清洁、素养和安全六个方面的管理,提高工作效率、减少浪费、改善工作环境及提高员工安全意识。然而,在实际操作中,车间6S管理的实施常常面临一些挑战。本文将深入探讨这些挑战,并提出相应的解决方案,以帮助企业更好地实施和优化6S管理。
1.挑战一:员工抵触情绪与不配合
问题分析:
在实施6S管理时,部分车间员工可能会对新管理模式感到抵触,尤其是那些长期习惯于传统操作流程的员工。许多人可能认为6S是额外的负担,尤其是在初期,需要投入大量时间进行整理、整顿和培训,这可能会导致部分员工不愿意配合,影响6S的实施效果。
解决方案:
-加强培训与沟通:企业需要通过定期的
6S培训和宣贯会议,使员工理解6S管理的意义和重要性,让他们意识到6S不仅仅是一个“清理整顿”的过程,更是提高生产效率和确保工作安全的重要手段。
-高层领导带头示范:高层领导和车间管理人员应该身体力行地参与到6S管理的执行中,为员工树立榜样。领导的示范作用能够极大地激励员工参与其中,减少抵触情绪。
-奖励与激励机制:设立6S执行效果的考核指标和奖励机制,鼓励员工在日常工作中保持6S管理的标准,通过物质奖励或精神激励提升员工的参与积极性。
2.挑战二:资源与时间的有限性
问题分析:
车间工作节奏通常较快,生产任务繁重,很多员工会认为6S管理是额外的负担,尤其是在整理和清扫环节。尤其是在大规模生产时,车间人员担心6S管理会占用大量的工作时间,影响生产效率。
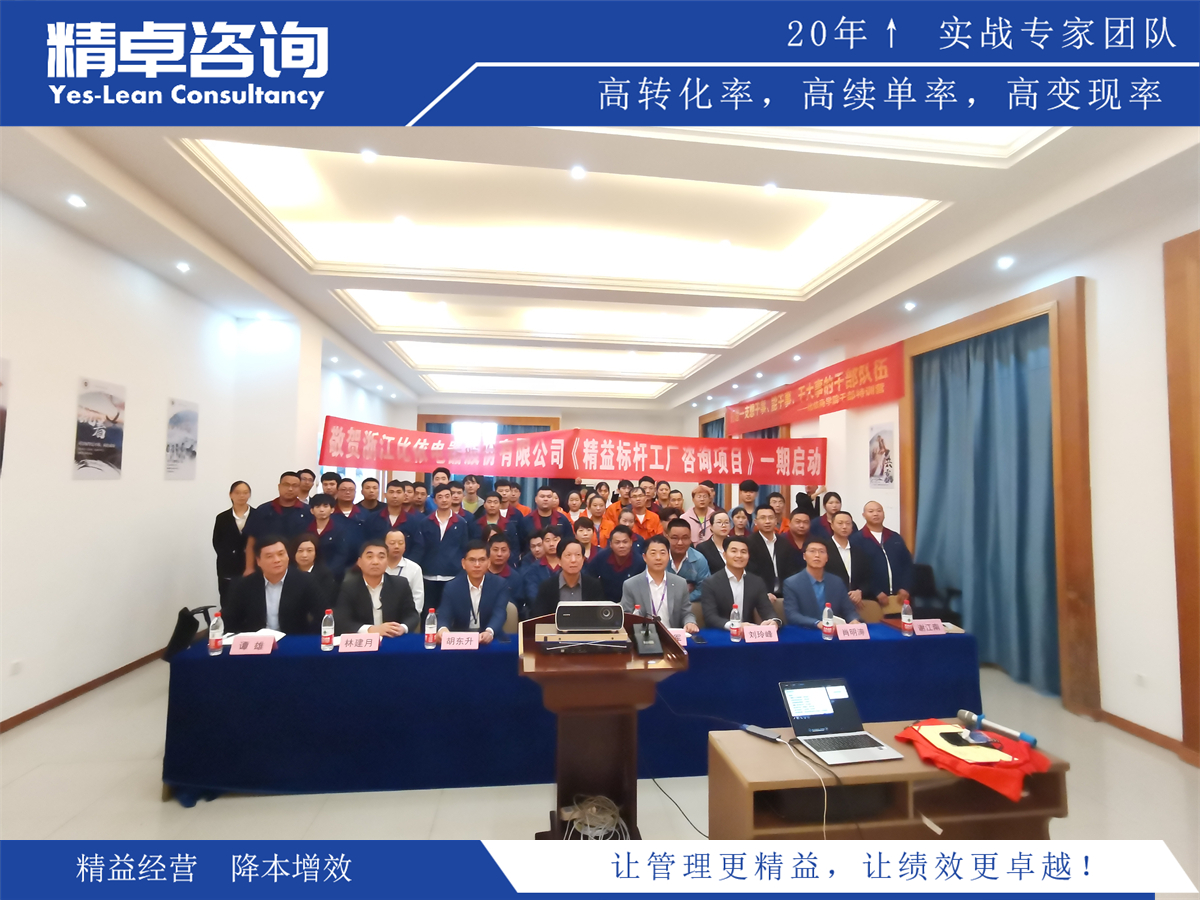
解决方案:
-制定合理的6S计划:企业应该根据车间的实际生产需求和人员配置,合理安排6S管理的时间。例如,清理和整理工作可以在非生产高峰时段进行,或者通过轮班制来保证6S管理与生产任务的平衡。
-分阶段实施:不必一次性要求车间全面执行6S管理,可以采取分阶段实施的方式,从最基础的整理和整顿入手,逐步推行到清扫、清洁、安全等方面,使员工逐步适应6S管理。
-精简流程,减少浪费:通过对现有流程的优化和合理设计,可以减少6S管理所需的时间。例如,通过合理布局生产线和工作站,减少不必要的物品搬运,提高操作效率。
3.挑战三:持续性与标准化管理困难
问题分析:
6S管理不仅仅是一个临时的活动,而是一个需要长期坚持和维护的过程。车间中的清扫、整理等工作往往会在初期得到较好执行,但随着时间推移,员工的积极性可能下降,6S管理的标准化和持续性执行会面临很大的挑战。
解决方案:
-标准化作业流程:在实施6S时,应确保每个环节都有明确的标准和流程。例如,清扫和整理的频率、清洁标准、工具摆放规范等都应书面化、标准化,员工依此执行,减少人为差异。
-定期检查与反馈:企业可以设置定期的6S检查机制,通过定期审核、检查和反馈,确保6S管理不间断执行。检查时应涉及所有员工和管理层,强调自查和互查的责任,确保员工在6S管理中的责任落实到位。
-现场看板与可视化管理:在车间区域内设置6S管理看板,明确显示各项标准和目标,并通过图表、标识等可视化手段持续督促员工保持整洁和规范,强化员工的长期遵守意识。
4.挑战四:设备和工具的管理与维护困难
问题分析:
在车间,生产设备和工具的数量庞大且种类繁多,设备的状态和工具的管理常常是6S管理中的薄弱环节。设备损坏、工具失散或难以找到等问题,常常导致车间效率低下,影响整体生产质量和安全性。
解决方案:
-设备与工具标识化:所有工具和设备都应进行标识,并制定统一的存放位置和规范。工具柜、工具架等存储设备应按照类别进行整理和标识,每个工具都有专门的“家”。
-定期维护和检查:对设备和工具进行定期检查和保养,确保设备处于良好的工作状态,并且及时发现和处理故障,避免因设备故障而影响生产。
-精益工具管理:引入
精益生产中的“5S工具管理”或“TPM(全面生产维护)”方法,建立设备维修保养的制度,提前预防设备故障,确保工具和设备的高效利用。
5.挑战五:安全隐患的管控
问题分析:
车间通常是一个复杂的工作环境,涉及到大量的机械设备和高风险操作,安全隐患较多。尤其是在实施6S管理初期,可能存在某些隐患没有及时被发现或得到有效控制,导致事故发生的风险增加。
解决方案:
-安全培训与教育:定期进行安全培训,教育员工遵守安全操作规程和规范,增强员工的安全意识和自我保护能力。培训内容不仅仅限于设备操作,还应涵盖6S管理中的安全要素,如物品堆放规范、走道畅通等。
-安全检查与隐患排查:在实施6S管理过程中,结合安全管理制度,进行定期的安全检查,发现潜在隐患并及时整改。可以通过建立安全隐患排查清单,列出每个岗位、设备的安全要求,确保全员参与到安全管理中。
-紧急应对机制:制定应急预案,确保一旦发生突发事件,员工能够迅速反应,减少损失和伤害。定期进行演练,提高员工的应急反应能力。
6.挑战六:员工参与度不足
问题分析:
6S管理的成功与否很大程度上取决于员工的参与度和执行力。如果员工对6S管理缺乏积极性,管理措施可能会流于形式,无法产生实际效果。
解决方案:
-建立员工参与机制:通过设立6S改进小组或工作小组,鼓励员工参与到6S管理的策划和执行中,让员工感受到自己在整个过程中扮演的重要角色。
-通过数据展示效果:通过定期展示6S管理实施的成果,如生产效率提升、事故减少、员工满意度提高等,用数据说服员工,激励他们更积极地参与到管理工作中。
-树立榜样:通过评选“6S优秀员工”或“最佳改进奖”,树立积极参与6S管理的榜样,鼓励其他员工向榜样学习,提高全员参与的积极性。
结语
车间6S管理在实际操作中面临的挑战是多方面的,但通过合理的管理措施、系统的培训、标准化操作和持续改进,这些挑战是可以有效克服的。6S管理的成功实施,不仅有助于提升车间的生产效率和安全性,还有助于营造更加健康、整洁和高效的工作环境,从而推动企业整体的持续发展和竞争力提升。