7S管理是对经典的
5S管理方法的扩展,包含了“安全”(Safety)和“节约”(Save),使得原本侧重于工作环境和流程优化的5S管理更加全面。7S管理不仅关注工作环境的整理、整顿、清扫、清洁和素养,还特别强调员工的安全意识和资源节约,旨在通过全方位的管理改善,提升车间的生产效率。本文将探讨
7S管理培训如何在车间生产中发挥重要作用,推动生产效率的提升。
一、7S管理中的“安全”提升生产效率
安全是7S管理中的核心要素之一。车间生产过程中,工人的安全直接影响到生产效率。如果生产环境存在安全隐患,可能导致工伤事故、设备损坏和生产中断,从而造成生产效率的大幅下降。通过7S管理培训,员工能够提升安全意识,及时发现并消除潜在的危险,避免事故的发生。
如何提升生产效率
-减少事故停产时间:通过安全管理的落实,员工能主动识别并消除安全隐患,从而减少因事故引起的停工时间。
-提高员工工作积极性:安全的工作环境能增强员工的信心和工作积极性,从而提升其工作效率。
二、7S管理中的“节约”提升生产效率
“节约”强调在资源使用、时间管理和成本控制上的高效利用。通过培训,员工可以更好地理解如何减少原材料浪费、减少生产过程中的空闲时间、优化设备使用率等,从而实现资源的最大化利用。
如何提升生产效率
-减少物料浪费:通过合理的物料管理和使用,避免过度采购或浪费,减少生产成本并提高经济效益。
-优化设备利用率:通过节约资源,避免设备长时间的闲置或不必要的维修,确保设备运行的高效性。
-提高时间效率:合理安排生产流程,减少生产中的等待时间和无效操作,提升整体生产速度。
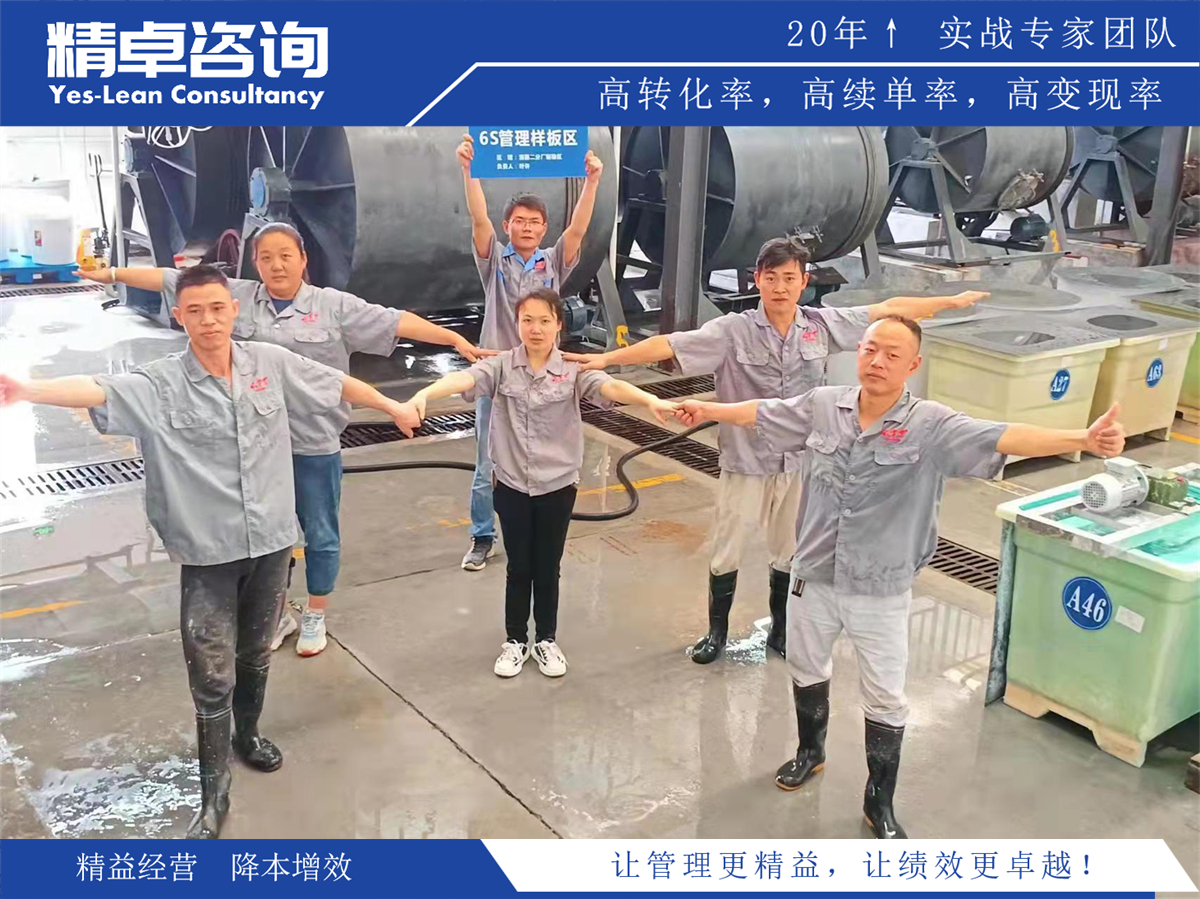
三、7S管理中的“整理”与“整顿”提升生产效率
整理和整顿分别强调清除无用物品和将物品按照一定标准摆放。在车间生产中,物品的有序管理可以大幅减少员工在生产过程中寻找工具、材料和设备的时间,提高工作效率。
如何提升生产效率
-提高空间利用率:整理和整顿通过清理不必要的物品,释放出更多的工作空间,使得员工能够更加高效地进行操作。
-减少寻找时间:将工具、材料按照使用频率和类别合理摆放,减少员工在生产中寻找物品的时间,从而节省时间并提高生产效率。
四、7S管理中的“清扫”和“清洁”提升生产效率
清扫和清洁不仅仅是物理上的清洁工作,还包括对设备和工作环境的维护。通过保持车间的清洁,能够确保生产设备处于良好的运行状态,减少故障率和停机时间,保障生产过程的流畅进行。
如何提升生产效率
-减少设备故障时间:定期清扫和维护设备,有效防止设备因灰尘、油污等问题发生故障,减少停机维修时间。
-提升员工工作效率:清洁和整洁的工作环境能提高员工的工作热情和效率,降低由于环境脏乱引起的心理压力和工作不便。
五、7S管理中的“素养”提升生产效率
素养是指员工自律、遵守工作标准和流程的能力。在7S管理培训中,素养的培养强调员工遵守7S管理的各项规定,形成自觉的工作习惯。员工的自我管理和持续改进意识有助于提升生产效率。
如何提升生产效率
-提高工作规范性:员工能够根据标准化的流程和规范完成工作,减少操作失误和返工,提升生产效率。
-推动持续改进:通过定期的7S培训和反馈,员工可以持续优化工作流程,减少无效操作,不断提升车间生产效率。
六、7S管理的综合效果对车间生产效率的提升
7S管理培训的实施,不仅能从多个维度提升车间的生产效率,还能促进员工的全面发展,创造一个高效、整洁、安全且节约的工作环境。通过全员参与的7S管理,车间生产的每个环节都得到了优化,从而提升整体生产效率和质量。
-提升生产速度:减少无效操作,优化资源配置,提高生产线的工作速度。
-提升产品质量:通过整洁的环境、规范的操作和及时的设备维护,减少生产中的质量问题和返工率。
-降低成本:通过资源的节约和浪费的减少,降低生产成本,提升经济效益。
七、总结
7S管理培训通过系统地培养员工的安全意识、节约习惯、工作规范和自我管理能力,有助于提升车间生产效率。通过整理、整顿、清扫、清洁、素养、安全和节约等方面的管理优化,企业能够减少浪费、降低故障、提高员工的工作效率,并推动持续改进,最终实现车间生产效率的全面提升。因此,7S管理不仅是一个简单的清洁工作标准,更是提升生产力、降低成本和提升产品质量的强大工具。