5S现场管理法是源自日本的一种高效生产管理方法,广泛应用于
精益生产、质量管理和企业持续改进中。5S通过对工作现场的整顿、清理和规范,帮助企业建立规范化、标准化的工作环境,进而提升生产效率、改善质量,并减少浪费。5S的核心目的是实现“高效、整洁、安全”的工作环境,帮助企业提升员工生产力、设备利用率和资源利用率。
5S的五个要素
5S是五个日文词的首字母缩写,每个字代表一个现场管理原则,它们分别是:
1.整理(Seiri,Sort):将现场不必要的物品、工具和材料清理出去,仅保留工作中必需的东西。
2.整顿(Seiton,SetinOrder):对必需的物品进行分类、定置和标识,确保易于取用,避免浪费时间。
3.清扫(Seiso,Shine):清洁工作现场及设备,保持环境的干净整洁,预防设备故障并保持良好的工作环境。
4.清洁(Seiketsu,Standardize):制定标准化的清洁与整理流程,确保5S活动能够长期保持。
5.素养(Shitsuke,Sustain):培养员工的习惯和自律,确保
5S标准能够持续执行,形成良好的工作习惯。
5S现场管理如何提升生产效率
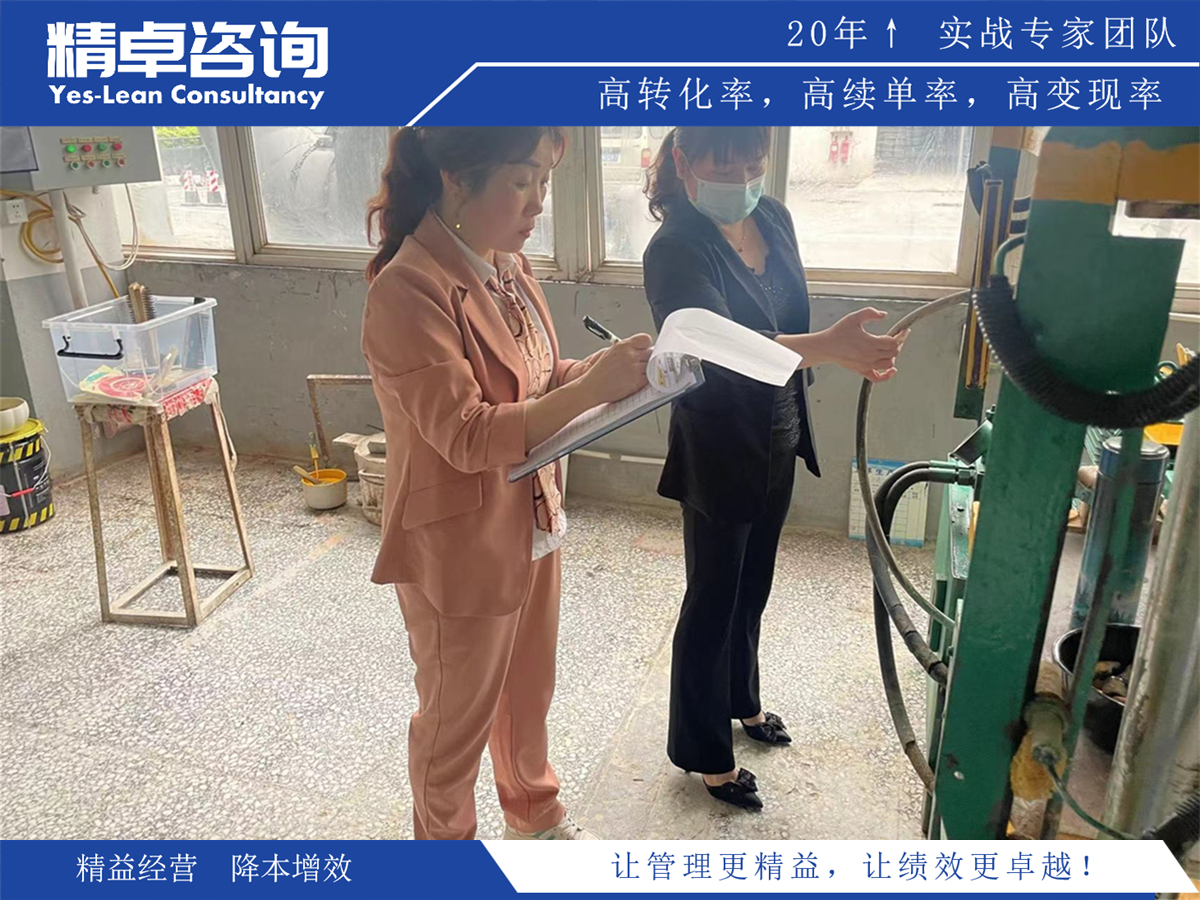
通过5S现场管理法的实施,可以显著提高生产效率。以下是具体的提升途径:
1.减少寻找时间和错误率
-整理和整顿可以帮助员工快速找到所需工具、设备和材料,避免浪费时间在寻找物品上。例如,通过工具定置、标签标识和明确的位置管理,确保每个工具和材料都有固定的存放位置,从而提高员工在生产过程中的工作效率。
-常见问题:没有标识或者工具乱放会导致员工浪费大量时间寻找工具,进而影响生产效率。
2.提高设备和工位的清洁度,减少故障停机时间
-清扫和清洁能够帮助消除设备的积尘和污染,减少由于设备故障引起的停机时间。保持设备的干净整洁,可以提高设备的使用寿命并保持设备运行的高效性。
-常见问题:设备长期不清洁会导致积尘、油污等影响设备性能,增加故障率和停机时间,降低生产效率。
3.减少无效的搬运和运输时间
-整理和整顿还帮助企业合理布局生产区域,减少不必要的物料搬运和运输。例如,将工具和原材料按生产线需求合理布局,减少工人走动距离和物料搬运时间,直接提升生产效率。
-常见问题:生产现场物料堆放混乱,工人需要频繁走动搬运,浪费大量时间在不必要的运输上,降低了生产效率。
4.标准化作业,提高生产流程的稳定性
-清洁和标准化能帮助企业为现场管理建立统一规范的操作标准,使员工在每个工作环节上都能按照标准作业,减少操作误差,提高工作的一致性和稳定性。
-常见问题:如果现场没有标准作业流程,员工在操作时容易出现不一致性,导致产品质量波动、操作效率低下。
5.降低事故发生率,提升员工士气
-素养培养员工良好的工作习惯,提升工作责任感。定期检查和维护工具、设备和工位的整洁状况,可以预防工作环境中的潜在安全隐患,减少安全事故。
-常见问题:现场不整洁、设备故障频发以及安全隐患没有得到有效管控,会导致员工的工作士气下降,甚至可能引发生产事故。
通过5S避免的常见问题
实施5S能够有效避免许多生产现场中常见的问题,以下是几个典型问题及其解决方案:
1.物料堆积与浪费
-问题:生产现场常常堆积大量不需要的物料和工具,导致浪费空间、增加寻找时间和物料损耗。
-解决方案:通过整理,对物料进行分类,清理掉不需要的物品。将必需物品按需求安排位置,实施定置管理,确保每个物品都有固定的存放位置,避免无序堆放和空间浪费。
2.设备频繁故障和停机
-问题:设备长期没有清洁和维护,容易出现故障,影响生产进度。
-解决方案:通过清扫和清洁,定期对设备进行清洁保养,减少设备故障率。制定定期检查计划,保持设备的良好运行状态,延长设备使用寿命。
3.生产环境凌乱和不安全
-问题:生产环境脏乱,可能存在工作区域不清晰、工具乱放和物料堆放不当的情况,不仅影响生产效率,还可能引发安全事故。
-解决方案:通过整顿和清扫,确保工作场所清洁整洁,所有工具、材料和设备都有明确的存放位置,减少事故的发生。通过素养,培养员工自觉遵守整理、整顿的良好习惯,保持工作环境的长期整洁。
4.员工的工作习惯差、执行力不足
-问题:没有规范的作业流程和现场管理标准,员工可能不按标准操作,导致生产效率低、质量差。
-解决方案:通过标准化作业(Seiketsu),制定标准化流程,并对员工进行培训,确保每个员工都能按照统一标准作业。此外,通过素养的培养,提高员工对
5S管理的认同感和执行力,确保5S持续执行。
5.频繁的物料缺失和超量库存
-问题:物料管理不当,导致物料过多或过少,增加库存成本或生产线停滞。
-解决方案:通过整理和整顿,根据生产需求设定物料的存放区域和数量,避免积压和短缺现象。通过及时检查和清理物料,确保库存管理的精确性。
5S的实施步骤
为了更好地实施5S现场管理,企业可以按照以下步骤进行:
1.领导支持与动员:高层管理者需要明确支持5S,制定实施方案并进行全员动员。
2.评估现状:在实施5S之前,评估当前工作现场的状况,找出问题所在。
3.制定5S计划:确定5S的实施范围和具体目标,制定详细的执行计划。
4.培训与实施:对员工进行
5S培训,确保每个员工了解5S的基本概念和实施方法。
5.持续改进:5S实施后,定期检查和评估执行效果,进行持续改进,确保5S管理长期有效。
总结
通过5S现场管理法,企业可以通过整理、整顿、清扫、清洁和素养的管理,消除工作现场的浪费和混乱,提升生产效率、改善工作环境、减少设备故障、提高员工士气。5S不仅能帮助企业优化资源配置,提升生产效率,还能创造一个更加安全、高效、整洁的工作环境,为企业的长期发展奠定坚实的基础。