一、引言
在当今竞争激烈的商业环境中,企业对生产现场的管理水平要求日益提高。
6S管理作为一种行之有效的现场管理方法,不仅能够提升企业的生产效率、产品质量,还能塑造良好的企业形象,增强员工的归属感和责任感。本文将深入探讨
现场6S管理的内涵、实施步骤以及其为企业带来的显著效益,为企业管理者提供一份实用的现场管理指南。
二、6S管理的内涵解析
(一)整理(SEIRI):优化资源配置的起点
阐述整理的核心在于区分现场物品的“要”与“不要”,及时清理不必要的物品,如废旧设备、过期物料等,为生产现场腾出宝贵空间,减少资源浪费,提高空间利用率,避免物品积压导致的管理混乱和效率低下。
(二)整顿(SEITON):构建高效有序的现场布局
解释整顿是对必要物品进行合理规划和定位摆放,并通过清晰的标识进行管理。例如,根据生产流程和物品使用频率,确定物品的存放位置和数量,使员工能够迅速找到所需物品,缩短取用时间,减少操作失误,提高生产效率和作业标准化程度。
(三)清扫(SEISO):营造清洁安全的工作环境
说明清扫不仅仅是保持现场的干净整洁,更重要的是通过清扫活动对设备进行日常维护和检查,及时发现设备的潜在故障和安全隐患,如设备的异常声响、松动部件等,从而确保设备的正常运行,延长设备使用寿命,为员工创造一个安全、舒适的工作环境,提升员工的工作积极性和工作质量。
(四)清洁(SEIKETSU):固化成果,形成长效机制
阐述清洁是将整理、整顿、清扫工作进行制度化、规范化,形成一套明确的标准和流程,并通过定期的检查和监督确保这些标准得到持续执行。例如,制定详细的6S检查表格和考核制度,明确检查的内容、时间和责任人,使6S管理工作成为企业日常运营的一部分,不断巩固和提升现场管理水平。
(五)素养(SHITSUKE):培育高素质的员工队伍
说明素养是6S管理的核心和灵魂,通过持续的培训、教育和激励措施,培养员工养成自觉遵守6S规定的良好习惯,形成积极向上的企业文化氛围。当员工将6S理念内化于心、外化于行时,他们会主动维护现场的整洁和秩序,积极参与企业的各项改进活动,为企业的发展贡献更多的智慧和力量。
(六)安全(SECURITY):筑牢生产现场的安全防线
强调安全在6S管理中的重要地位,包括识别和消除现场的各类安全隐患,如不安全的操作行为、危险的工作区域等,制定完善的安全操作规程和应急预案,加强员工的安全意识培训,配备必要的安全防护设施,确保员工的人身安全和企业的生产安全,实现企业的可持续发展。
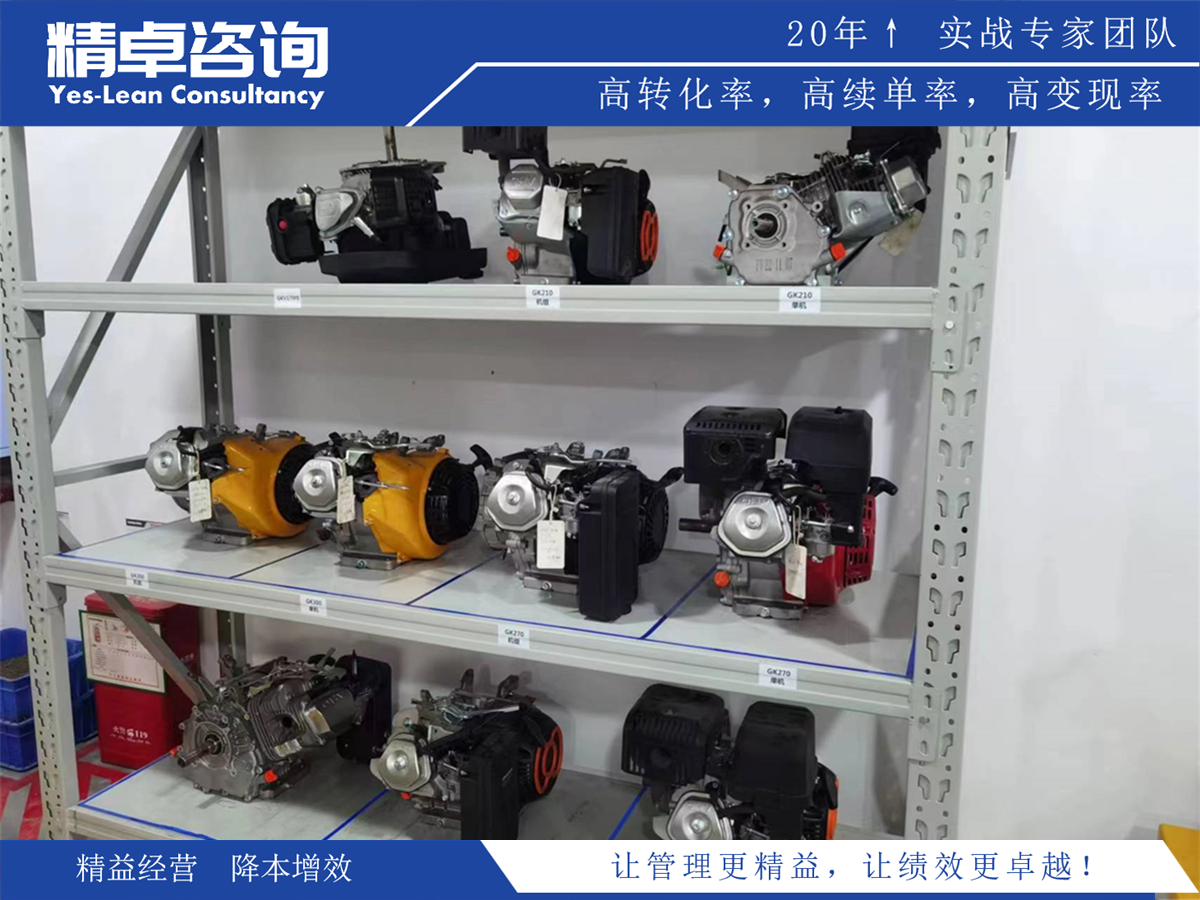
三、现场6S管理的实施步骤
(一)项目启动与规划
成立6S管理推行领导小组,明确各成员的职责和分工,确保推行工作的顺利开展。制定详细的
6S推行计划,包括目标设定、实施步骤、时间节点、资源需求等,为推行工作提供明确的指导方向和行动纲领。
(二)宣传与培训
通过多种渠道,如内部宣传栏、培训会议、视频教程等,广泛宣传6S管理的理念、方法和重要性,使全体员工充分认识到6S管理对企业和个人的积极影响,提高员工的参与度和积极性。同时,针对不同岗位的员工开展有针对性的
6S培训,使员工掌握6S管理的具体操作方法和技巧,为实施工作奠定坚实的基础。
(三)现场诊断与问题分析
对生产现场进行全面的调研和诊断,详细记录现场存在的各种问题和不足之处,如物品摆放杂乱、设备清洁不到位、安全标识缺失等。运用5Why等方法对问题进行深入分析,找出问题的根本原因,为制定针对性的整改措施提供依据。
(四)整理与整顿实施
按照整理的原则,对现场物品进行全面清理,划分“要”与“不要”的物品区域,将不要的物品及时处理掉,对必要的物品根据使用频率和类别进行分类整理。然后,依据整顿的要求,对整理后的物品进行合理布局和定位摆放,设置清晰的标识牌和区域线,确保物品摆放整齐、有序、易于取用。
(五)清扫与清洁推进
制定详细的清扫计划和标准,明确清扫的区域、内容、责任人以及清扫的频率和方法。对生产现场进行全面清扫,包括地面、设备、工具、墙壁等各个角落,同时对设备进行日常维护和保养,记录设备的运行状况和维护情况。在清扫工作的基础上,将整理、整顿、清扫的成果进行制度化和规范化,制定完善的6S检查制度和奖惩机制,定期对现场进行检查和评估,确保各项工作得到持续改进和保持。
(六)素养与安全强化
通过持续的培训、教育和激励措施,培养员工的6S意识和良好习惯,将6S管理融入到员工的日常工作中。定期开展安全培训和演练,提高员工的安全意识和应急处理能力,加强现场的安全管理和监督检查,及时消除安全隐患,确保生产现场的安全稳定运行。
四、6S管理为企业带来的效益
(一)提升生产效率
通过优化现场布局、减少物品寻找时间、提高设备运行效率等措施,6S管理能够显著缩短生产周期,提高企业的生产效率和产能,满足市场需求,增强企业的市场竞争力。
(二)提高产品质量
整洁有序的生产现场、规范的操作流程和良好的设备维护状态,有助于减少产品生产过程中的错误和缺陷,提高产品的一致性和稳定性,提升产品质量,降低废品率和返工率,从而提高客户满意度和企业的品牌声誉。
(三)降低成本
6S管理通过减少库存积压、降低设备故障率、提高物料利用率等方式,有效降低企业的生产成本,包括采购成本、库存成本、维修成本等,为企业创造更多的利润空间。
(四)塑造良好企业形象
一个实施6S管理的企业,其现场整洁、秩序井然、员工素质高,能够给客户、合作伙伴和社会各界留下良好的印象,提升企业的知名度和美誉度,为企业的发展创造有利的外部环境。
(五)增强员工凝聚力和归属感
员工在一个干净、舒适、安全的工作环境中工作,能够感受到企业对他们的关怀和尊重,同时通过参与6S管理活动,员工的自身价值得到体现,团队协作能力得到提升,从而增强员工的凝聚力和归属感,减少员工流失率,稳定企业的人才队伍。
五、成功案例分享与经验借鉴
(一)案例介绍
以某知名制造企业为例,详细介绍该企业在实施6S管理前后的现场状况、生产效率、产品质量、员工士气等方面的变化情况。展示该企业在6S推行过程中采取的具体措施和方法,如如何开展整理整顿工作、如何建立清扫清洁标准、如何提升员工素养和加强安全管理等。
(二)经验总结
从领导重视、全员参与、持续改进、制度建设等多个角度总结该企业成功实施6S管理的关键经验和启示,为其他企业提供有益的参考和借鉴,帮助企业少走弯路,顺利推进6S管理工作,实现企业的可持续发展。
六、结论
现场6S管理是企业提升管理水平、增强竞争力的重要手段。通过深入理解6S管理的内涵,按照科学的实施步骤稳步推进,并持续关注和改进,企业能够充分发挥6S管理的优势,实现生产现场的规范化、标准化、高效化,为企业的长远发展奠定坚实的基础。在未来的发展中,企业应不断深化6S管理理念,将其与企业的战略目标相结合,不断探索创新,推动企业管理水平再上新台阶,在激烈的市场竞争中立于不败之地。