7S管理作为一种
精益管理方法,在传统的5S基础上进一步扩展,特别适用于生产、仓储、办公等多种环境。7S管理法通过对工作场所进行系统化、精细化的管理,全面提升工作效率、减少浪费、优化工作流程、改善员工工作环境,是推动企业持续改进的重要工具。
什么是7S管理?
7S管理是在传统
5S管理的基础上,增加了两个要素,即“安全”(Safety)和“节约”(Save),因此形成了“7S”管理体系。7S管理的核心目的是通过系统化的管理、细致的标准化、持续的改进,不仅提升生产效率,还可以改善员工的工作环境、增强团队协作和工作满意度。
7S管理的七个要素
1.整理(Seiri):
-定义:整理是指将工作场所中的物品按需进行分类,去除不必要的物品,避免物品堆积、浪费空间。
-目的:减少无关物品的干扰,腾出空间,使常用物品易于获取。
2.整顿(Seiton):
-定义:整顿是指将必要的物品按照使用频率、重要性等进行合理的规划和摆放,确保物品取用方便,存放有序。
-目的:通过合理布局、清晰标识,减少寻找物品的时间和无效的操作。
3.清扫(Seiso):
-定义:清扫是指对工作环境、设备、工具进行定期清洁,保持车间、办公场所等区域的清洁整洁,减少灰尘和污染。
-目的:防止设备故障、生产事故,确保工作环境干净、舒适。
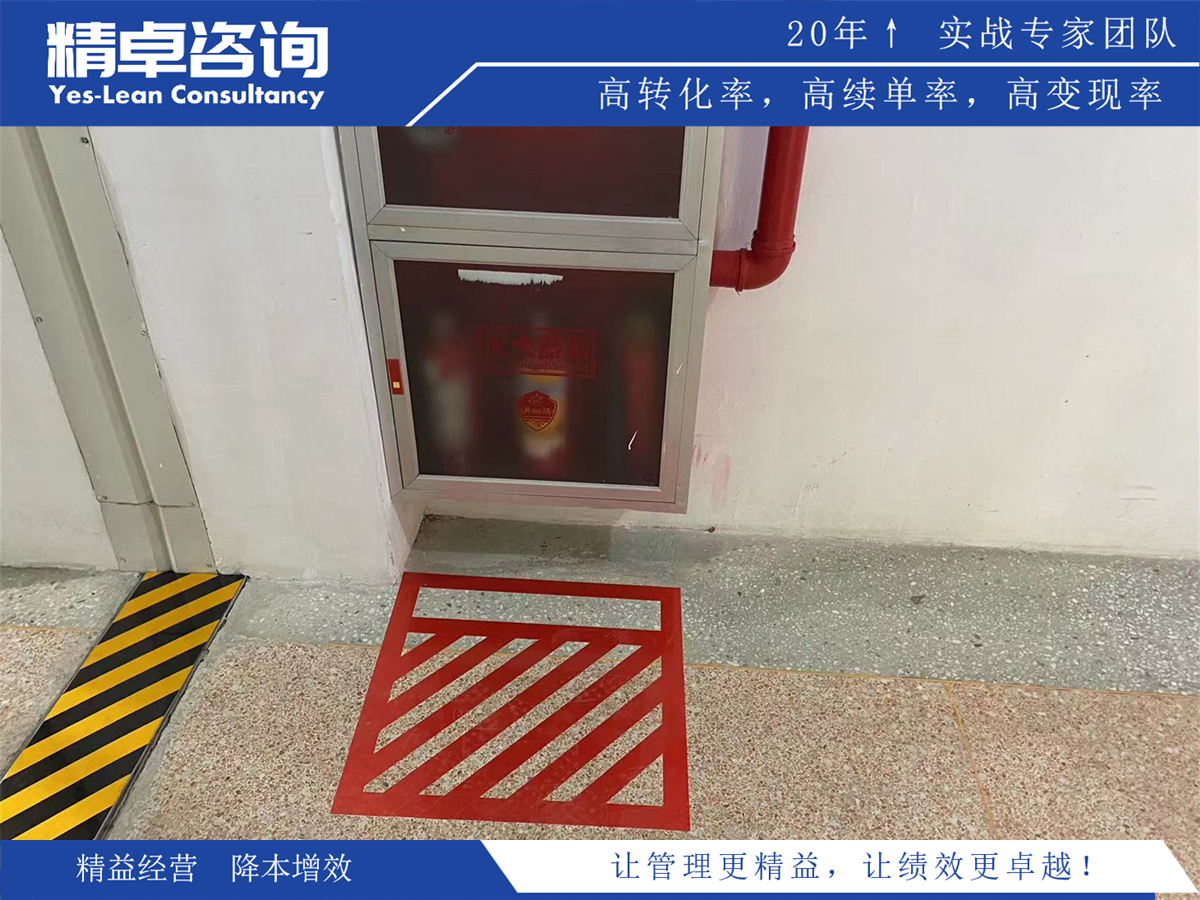
4.清洁(Seiketsu):
-定义:清洁是指对整理、整顿、清扫的结果进行标准化,并确保持续性执行,使良好的工作环境和秩序得以长期保持。
-目的:通过规范化流程、标准化操作,确保前述措施得以长期执行,避免回到混乱的状态。
5.素养(Shitsuke):
-定义:素养是指培养员工自律的工作态度,养成良好的工作习惯,使其自觉遵守规范,不断自我提升。
-目的:通过定期培训、督导、激励等措施,使员工逐渐形成自我管理、自我约束的意识,确保5S的长期执行。
6.安全(Safety):
-定义:安全管理指的是为防止各类事故的发生,对工作环境和生产设施进行规范化管理,确保员工和生产过程的安全。
-目的:通过消除安全隐患、加强风险防控,确保员工和设备的安全,避免因意外事故带来的损失。
7.节约(Save):
-定义:节约是指通过合理利用资源(如时间、物料、能源等)来减少浪费、降低成本,提升资源使用效率。
-目的:通过优化流程、减少浪费、提高设备和物料的利用率,实现成本节约和效益提升。
7S管理的实施步骤
为了有效实施7S管理,企业需要系统地组织、协调并逐步推进每一个环节。以下是7S管理的详细实施步骤:
1.准备阶段:动员与培训
-领导支持:首先,企业高层管理层需要对7S管理给予足够的重视,确保充分的资源支持和领导关注。
-团队建设:组建专门的7S管理团队,负责整个实施过程中的策划、协调、推进和监督。
-员工培训:对全体员工进行7S管理理念、目标和具体操作的培训,帮助员工理解7S的意义和具体实施方法。
2.第一步:整理(Seiri)
-清理不必要的物品:对车间、办公室及仓库中的物品进行分类,判断哪些是必需品,哪些是多余或过期的物品。清理过期物料、未使用设备等,减少空间浪费。
-分类管理:将有用的物品分类存放,无用的物品及时处理,减少占用的空间。
实施技巧:
-使用标签、标识等方式明确物品的状态和用途,做到一目了然。
-定期进行“整理日”,确保每个员工都参与物品清理和分类,避免物品积压。
3.第二步:整顿(Seiton)
-合理安排存放位置:根据使用频率、物品重要性对工具和设备进行合理布置,常用物品放在方便拿取的地方。
-标识管理:对所有物品进行清晰标识,设置储物柜、货架等,让员工一目了然地知道物品的存放位置。
实施技巧:
-设立标识区域,利用色标、标签、条形码等方式帮助员工快速找到需要的物品。
-制定统一的物品存放标准,使物品归类更加系统化。
4.第三步:清扫(Seiso)
-清洁工作环境:保持车间、办公室、生产设备的清洁,定期对设备进行清洁、检查和保养,避免因积尘、油污影响设备运作。
-清扫责任:指定专人负责清扫工作,确保清扫不留死角。
实施技巧:
-制定每日清扫计划,定期对车间地面、设备、工具等进行彻底清洁。
-通过定期检查设备,确保设备的清洁状况良好,避免故障影响生产。
5.第四步:清洁(Seiketsu)
-标准化清洁流程:制定标准化的清洁操作规程,包括清洁频率、清洁方法和检查标准,确保车间、设备、工具的清洁工作长期维持。
-建立清洁检查制度:定期检查5S执行情况,确保清洁标准得以贯彻。
实施技巧:
-为每个区域、设备设置清洁周期和责任人,确保每项清洁任务都有具体的执行人。
-定期对员工进行清洁流程的复训,确保清洁工作不因疏忽而松懈。
6.第五步:素养(Shitsuke)
-培养员工自律性:通过培训、督导和激励,培养员工良好的工作习惯,让每个人都能够自觉遵守7S管理规定。
-持续改进:在日常工作中,定期评估7S执行情况,发现不足及时改进。
实施技巧:
-通过表彰和奖励制度,鼓励遵守7S标准的员工。
-开展7S评比活动,评选优秀团队和个人,形成良好的竞争氛围。
7.第六步:安全(Safety)
-安全隐患排查:定期进行安全检查,消除车间、生产设备等存在的潜在安全隐患,确保员工的工作环境符合安全标准。
-制定安全规范:建立明确的安全操作规程和应急预案,确保员工在工作中始终遵守安全操作标准。
实施技巧:
-设置安全标识、紧急疏散通道、灭火设备等,确保所有员工都能迅速应对突发情况。
-定期组织安全培训和应急演练,提高员工的安全意识。
8.第七步:节约(Save)
-节约资源:通过优化工作流程、减少浪费、提高设备和物料的利用率来降低成本。
-提高效率:通过流程改进和设备维护,减少生产过程中的能源消耗,提升整体效率。
实施技巧:
-通过
精益生产工具(如价值流图分析、瓶颈分析等)识别流程中的浪费环节,持续改进。
-采取节能措施,优化生产过程中的能源使用,降低能源成本。
总结
7S管理是一个从基础管理到持续改进的系统化过程,它不仅涵盖了传统的5S管理,还增加了“安全”和“节约”两个关键要素。在实施过程中,通过合理规划、标准化操作、员工素养提升等方式,7S管理能够帮助企业优化工作环境、提升工作效率、降低生产成本,同时提高员工